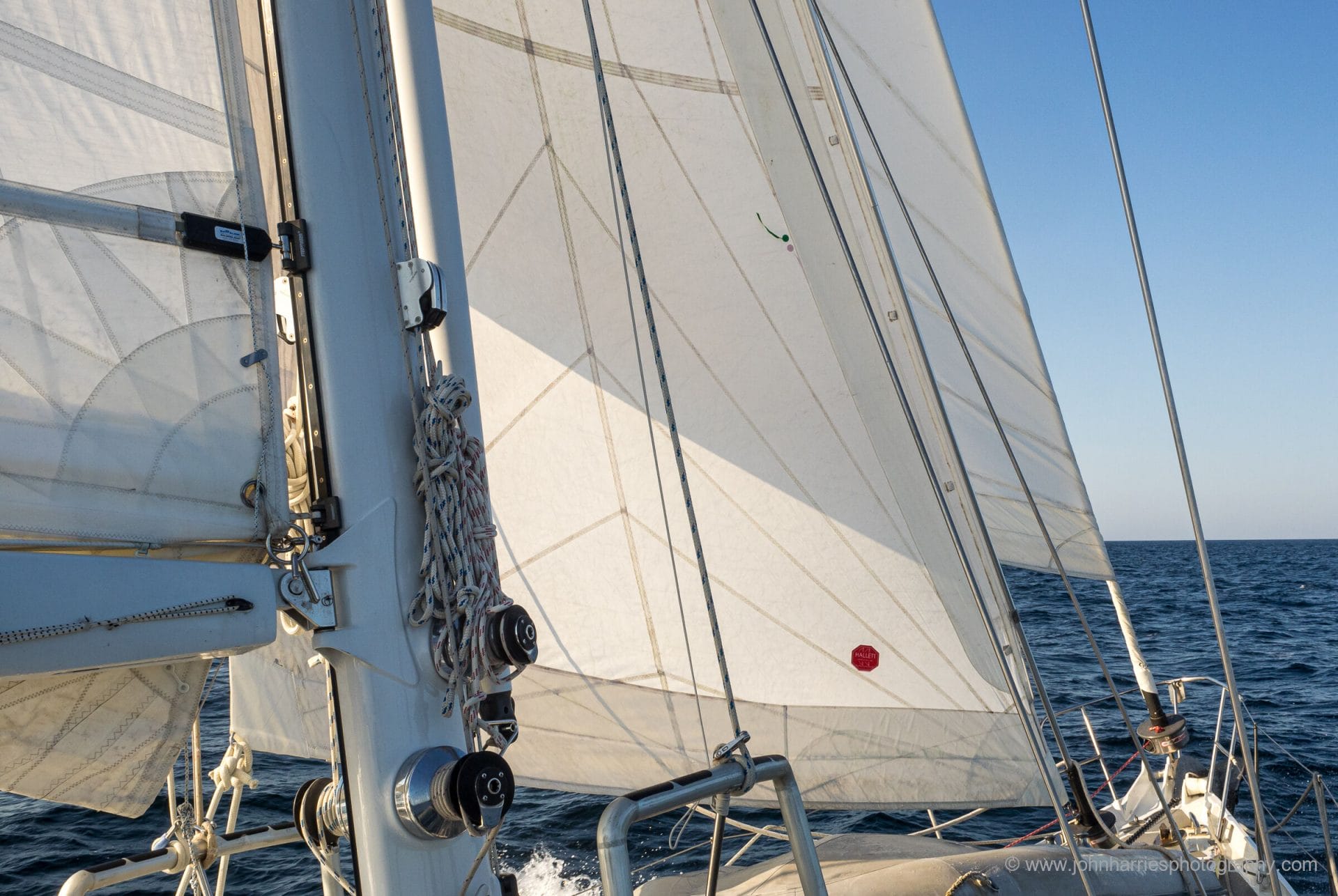
After four…count ’em, four…in-depth rig inspection articles:
We are now on the fifth and final before the downloadable checklist.
Seems crazy that it took that much detailed writing to get here. I figured two in-depth articles, three tops, would cover it. But now we are nearly done, I realize it actually makes sense that this was such a big task.
The rig is one of the big five things that really matter when we go offshore, and the one with the most details to get right, and keep right.
And the rig is also, more than any other system, the one where the failure of just one piece, perhaps just a toggle, can have the most disastrous and hardest-to-fix consequences—there’s no fixing a dismasting at sea.
It’s worth the effort to inspect this stuff right…and write 14,000 words about it. Or, at least it feels that way…now I’m done.
Let’s get it finished:
Very similar for ProFurl but all their foil joints have split bearing inserts making it easier.
Red loctite recommended on the foil to sleeve set screws also. You don’t want these loosening, ever.
Rinse the swivel and drum assemblies regularly. The seals are well designed and the grease can last 10 years (easy on the swivels up high) but if you don’t service the drums every 3-5 years by removing seals and cleaning and lubricating bearings then at 10 years when you really MUST service these you’ll find you likely need a bearing and seal replacement kit.
Kits include circlips, seals, bearings and grease. Not hard to replace as the ProFurl drums come off easily due to their simple design.
If you were following the 3-5 year service/inspect then maybe you’ll have no problem with the disassembly since you removed the screw/bolts and cleaned them up. 10 years? maybe some frozen bolts to contend with.
Parts available from Wichard/ProFurl, in the US I find Vela and Mauri Pro good parts distributors. You can also find OEM specs for bearings and seals online if you want to go that route and save a few dollars.
Bottom line on ProFurl is maintenance. wait much more than 10 years and the bearings just rot and frag then it is no fun. It will still furl, maybe, using a winch and likely destroying the bearing races, now that’s expensive.
Good information. It seems the new ones aren’t as well made as the old ones. We swapped ours old one (35 years +?) when we couldn’t find a replacement for a damaged foil section. The drum and swivel bearings on the old one were still perfect.
Hi Jeffrey,
That’s great information, just the kind I’m hoping for. Thank you!
Does anyone know if it’s possible to pull a new wire through a furler by sticking the ends together with epoxy?
(For when there isn’t a handy welder)
Possibly overlapping core and outer wraps for greater surface area.
I would have thought this would provided enough strength?
Hi Dn,
I doubt that epoxy would stick to wire well since there are always traced of oil on the strands left over from the manufacturing process. So, if I were going to try an adhesive it would be Plexus, not epoxy, given that I have has good luck sticking to stainless with zero preparation with the latter: https://www.morganscloud.com/2008/02/01/plexus/
While I certainly wouldn’t recommend it, as there’s usually a welder around anywhere you’ve got the mast down, it will take less than 15 minutes to do it properly. That being said if you absolutely HAD to, I would think of using a plexus adhesive, or testing out the Devcon Plasti-weld. I was told it is actually rebranded plexus in a small retail package, it is definitely a methyl-acrylite and seems to do the trick where epoxy doesn’t. If I really didn’t want to be dealing with it coming apart halfway inside the foil, I would grind the tips down to a taper, and wrap a bit of glass in there with the glue.
Thanks for this series of maintenance and inspection articles.
Regarding the Tides Marine track: I had one installed on my 36 ft sloop in 2010 and it performed very well including during a cruise in Mexican waters, and two round trips between California and Hawaii. I had no problem downwind reefing, which was a main goal for having the track. When I let the halyard loose, the main dropped like a rock. When the track was installed, I secured it to the mast to prevent movement using ~6 inch long Sikaflex beads about every 3 or 4 ft. Earlier this year I had the mast down and standing rig replaced. The Sikaflex had held, but the 12-yr old Tides track was trash; it cracked badly in places as I pulled it off the mast, and it was not hard to break it apart with my hands. I shuddered to think what might have happened if the track had failed and the main luff had come off while sailing. A sample of the track was sent to Tides and they said it was UV damage and it needed to be replaced, which I did. Tides Marine thinks it’s normal and expected to replace their track after about 10 years. I don’t see that caveat in their literature. Here’re some images of the old track: https://photos.app.goo.gl/VmTE6yiHsdrW3zr19
Hi Steve,
Good idea on securing the tides track. And thanks for the heads up on the UV degradation. Both very useful updates hat I will add in when I do my final edit on all this.
Furlex Type D (now Selden) on my boat. It’s getting on a bit old now, hence serviced every 2 years by my local rigger. To routinly lubricate it is a dab of grease in 7 places. I use a large, plastic syringe, about 500 ml size and pack it with the correct grease. The syringe size is based on the plastic nozzle size which can be pressed into the grease hole and a seal made, not the volume of grease. With a bit of pressure a small bead can be injected injected into the bearing. I try and force grease in at rate equal to match the bearing rotation speed so that each race gets a light coating, full circumference, instead of ramming a large dob into the race. The syringe makes this easy and mess free.
The system is +20 years old, so I am thinking of replacing it.
Hi Alastair,
Thanks for that, very useful, particularly given how many Furlex units there are out there.
Leisure Furl / Forespar publish a manual with maintenance schedule for our in-boom reefing system:
https://www.forespar.com/pdf/leisure-furl-owners-manual.pdf
Maintenance is in many ways similar to head-foils, with the advantage that everything is carried out at deck level. Main things we have learned as follows:
Regular (3->6 months) fresh-water wash down front and back of mandrel and coating of PTFE lubricant on the mainsail luff tape where it runs in the mast track. If the halyard or furling rope starts to make lots of noise (strain) on the winch, then we know it’s time to wash down / lube again.
Ev 24-36 months (or whenever our mainsail goes in the shop for service), support the mandrel weight and remove the shaft through the mast, clean and grease shaft and bearings.
These booms are significantly heavier than conventional booms, so very important that:
Tips:
We are still learning, but as a whole any extra maintenance is out-weighed by the benefits to us – much the same our roller headsail.
Hi Rob,
I was hoping you would come up with your experience. Thank you!
It always amazes me that manufacturers don’t make more use of thread inserts (Helicoils). As an aluminium boat owner I came to love the things. What brand of PTFE lubricant do you use? I have always had good luck with McLube Sailkoat for that kind of thing.
I usually buy whatever PTFE spray I can get from a local hardware/auto-part store. Haven’t noticed any practical difference between generic and the Harken McLube (except price). Anyone know if there is an actual difference..?
I have been considering making a track cleaning “slug” from a 300 mm section of old luff tape, and a disposable cleaning J-cloth attached (soaked in a wash-detergent mix). With an eyelet top and bottom, attach the halyard and a downhaul to hoist / retrieve several times to clean out the inside of the track, perhaps once a year?
Any thoughts / experience from your sailmaker days on cleaning inside foil tracks John? Thanks, Rob
Hi Rob,
Back in the day when I was sailmaking we used to make up short lengths of luff tape with an eye in either end so crews could haul them up and down the headstay foil grooves to clean them out. That said, I’m not sure it did that much good, particularly since these were boats that did a bunch of sail changes, so were keeping the track clean anyway.
With headstays I have always found a good spray of McLube on the tape as we hoisted the headsail at the beginning of the season was all it needed to be free running even a couple of months later. In fact I would say that the availability of McLube was a breakthrough in ease of hoisting,
So my guess would be that the same treatment once a month or so would keep the Leasurefurl track free running without the need for specific cleaning.
As to whether or not Mclube adds anything over and above generics, I just don’t know. But given the critical nature of your usage, I guess I would default to Mclube since, while it’s expensive, the cost is trivial when compared to the unit being serviced.
Hi John, good point about the frequency of track usage. A benefit of this system is how quick it is to prepare and hoist the sail, which means we use our main all the time, unless there is absolutely no wind.
So good reminder – I’ll increase the frequency of treatment as you suggest.
Hello John,
Thanks for another thorough article. I have a question on what you mean by “tracks and sliders usually supplied as standard”. Would you consider that an Antal HS24 track and slider system is “standard” and therefore worth considering replacing on a 47-ft, 13 tonne sailboat? Do you think the improvement in mainsail handling would be worth it and should a roller bearing system be considered instead?
Hi Alain,
I do not know of any slippery track being standard: the Antal and Harken are likely just too expensive.
I have the Antal system (12m/15 ton+ live-aboard weight), and while I have no direct experience with roller bearing systems, I have lots of friends with mostly Harken RB systems and, in conversation and comparing impressions, I have heard no difference in performance.
Mine is pushing 25 years old/70k miles now and have had no problems.
I consider slippery track not only a large improvement in mainsail handling, but also an impressive safety improvement as I can reef and douse the main without rounding up.
I also consider slippery track as essential gear for passage-making sailboats.
My best, Dick Stevenson, s/v Alchemy
Hi Alain,
Good question, I was not clear enough. What I meant was just an an ordinary track, typically part of the aluminium extrusion, with slides running up and down it.
As to the Antal HS24, that looks like a nice system, and given that your boat is reasonably light for her length, I’m guessing it should be fine, with no good reason to upgrade to a roller bearing system.
All that said, the key test is can you reef and un-reef relatively easily while sailing off the wind without having to round up and rag the main. If so, all is good.
Thanks John and Dick for these comments. I can effectively reef and douse the main without rounding up, other than when I’m sailing dead downwind in very strong winds, so I guess I’ll leave well enough alone!
Hi Alain,
It is exactly that scenario where I most appreciate slippery track: dead down wind in very strong winds.
I have reefed the main progressively DDW wing and wing putting in a third reef in near gale (B7) conditions and later dousing the main altogether in gale (B8) conditions. It was a day of just steadily increasing winds.
In setting the three reefs and eventual dousing of the main, all was done on a relatively steady un-heeled platform perfectly safely. There was no rush as there was no flogging of the sails nor any safety issue. The lowering was done incrementally, took time, but all was done without flogging the sail and the boat just kept charging along under control.
It is in heavy air downwind where I consider slippery track a boon to safety, especially for couple cruising.
My best, Dick Stevenson, s/v Alchemy
We have a ProFurl genoa furling system. I had top and bottom swivels rebuilt by Pacific Offshore Rigging in San Diego in 2016 after about 20 years of coastal cruising. That was a preventive measure for offshore work, since it still worked very well. I have friends who have rebuilt their profurls, but it is a little complicated. Pacific Offshore really knows its stuff. More recently, my top swivel got misaligned and the only solution was to replace the upper swivel for $1,000. Pacific Offshore says it has seen the problem a half dozen times in the last 15 years. The part is now redesigned to eliminate the issue, but may have new ones I cannot predict. You cannot inspect the bearings on the ProFurl, of course, without taking everything apart. Pacific Offshore told me that all main company systems have pros and cons. Nonetheless, when maintained, as John says, they have made short-handed sailing much easier.
Hi Terence,
Thanks for the real world experience based tips, always the best source.